Pérenniser l’exploitation ! Tel fut le point de départ de la réflexion en 2010 pour la création d’une unité de méthanisation au GAEC de l’Union. Objectif : apporter des revenus complémentaires et valoriser les matières organiques de la ferme et uniquement celles-ci, par volonté d’autonomie !
Un GAEC plein d’énergie
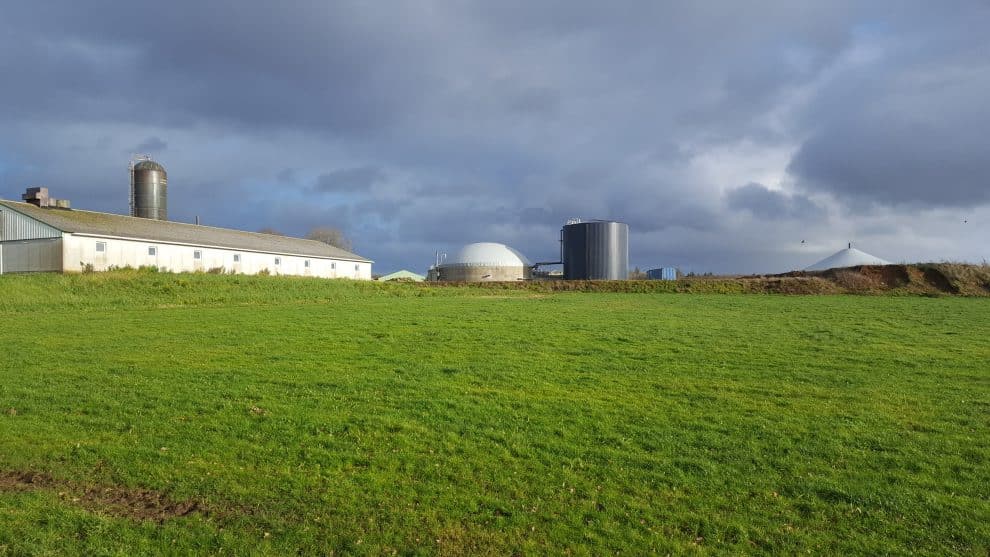
Le GAEC de l’Union a été créé en 1963, avec cinq associés, à Pommerit-le-Vicomte, dans les Côtes‑d’Armor, pour une production de porcs et de vaches laitières. Dès 1974, les cinq associés ont la fibre énergétique avec la création du premier silo-tour de 500 t de stockage de maïs, suivi d’un deuxième permettant d’économiser alors 27 000 l de fioul/an. En 2003, le GAEC met installe en porcherie des échangeurs pour récupérer la chaleur avec un delta de 13 °C. Puis, en 2010, c’est la mise en place d’une centrale photovoltaïque de 53 KW sur la stabulation. « En 2010, les revenus porcins et laitiers n’étaient pas suffisants, explique Frédéric Page, fils d’un des premiers associés qui a rejoint le GAEC en 1988. Nous voulions augmenter les revenus sans pour autant augmenter le cheptel. En parallèle, avec nos 500 truies et 70 vaches laitières, sur 300 ha, nous avions un potentiel d’intrants important pour un digesteur. Nous avons donc naturellement réfléchi à la possibilité de créer une unité de méthanisation, d’autant que les contrats en cogénération sont garantis sur 20 ans, ce qui n’est pas le cas des prix du porc et du lait ! »
Une panse en béton !
« Nous avons commencé par visiter un salon de méthanisation dans les Ardennes puis avons multiplié les visites d’unités de méthanisation, poursuit Frédéric Page, avant d’entamer une étude de faisabilité en 2014 avec la chambre d’agriculture des Côtes‑d’Armor, notre centre de gestion, l’ADEME et l’association Aile. Nous avons certes pris le temps, près de 9 ans avant la mise en service, mais la mise en place d’une unité de méthanisation ne s’improvise pas. Nous avons fait la démarche de visiter d’autres unités et de consulter les chambres pour bien savoir ce que nous voulions faire avant de contacter un constructeur (qui aurait pu nous influencer si nous n’avions pas eu d’idées précises !). Une grande partie de nos réflexions fut de savoir quel type de méthanisation nous souhaitions avoir. Si l’on veut monter une unité de méthanisation, il est nécessaire de prendre ce temps de voir ailleurs. Si vous n’avez pas le temps, alors vous n’aurez pas le temps de vous occuper de votre méthaniseur ! »
« Notre premier objectif était d’être autonomes. Nous avons dimensionné l’unité de méthanisation en fonction de ce que nous produisions. » La production a été lancée début 2019 et ce sont presque 30 t par jour qui sont intégrées dans le digesteur : 6 à 12 t de fumiers, 20 m3 de lisiers, 2 à 3 d’herbes, 500 kg de menue paille (la ferme est équipée d’une moissonneuse-batteuse qui la récupère), 4 t de rafles de maïs, 3 t d’ensilage de seigle et une part de recirculation du postdigestat. « Je travaille la ration comme je nourris le troupeau de vaches, explique Frédéric Page. C’est une ration “bretonne”, diversifiée, et non la ration allemande unique au maïs. Selon la période de l’année, celle-ci va différer en fonction de nos productions (CIVE par exemple). Il faut faire des transitions comme avec les bovins : une méthanisation, c’est un peu une panse en béton ! » Pour les intrants, le GAEC a joué la prudence en ne comptant pas sur l’ensilage de maïs. Une réserve potentielle qui pourrait servir par exemple au cas où la récolte de CIVE ne serait pas aussi bonne, après un automne trop pluvieux, comme cette année par exemple.
Préfosse pour ration bretonne
« Nos rations étant diverses et variées, nous avons assez vite souhaité lors de nos visites que les matières entrant dans le digesteur soient préalablement préparées. C’est pourquoi nous avons fait le choix d’installer une fosse de réception en amont. L’incorporation directe correspond plus, à notre avis, à des intrants de types ensilage. » La fosse est reliée à un poste de mélange (étape d’hydrolyse), le tout permettant une autonomie d’intrant de 2 à 3, voire 4 jours. « Nous avons ainsi une préparation homogène liquide, avec un système de blocage des cailloux et d’une partie des sédiments. Nous connaissons une installation à incorporation directe qui est obligée de vider d’importants tonnages de cailloux et de sédiments, un volume qui en plus occupe une partie du digesteur pour rien. »
Le GAEC a réalisé en autoconstruction la partie ouvrage en béton et a retenu la société Kerboas-Cdeai comme constructeur de l’unité, celle-ci préconisant toujours un système de mélange, digesteur et postdigesteur, ainsi qu’un système d’agitation non mécanique. « Pour ce qui est de la conception, nous proposons une pompe à la base du digesteur qui aspire et ramène le digestat, créant ainsi une agitation, mais sans système d’agitateurs à pales, plus fragiles, car cela supprime tout élément mécanique dans le digesteur, précise Landry Aubert, responsable technique de Kerboas-Cdeai. Le temps de séjour en mésophile (utilisé en injection biogaz) est plus long et nécessite un digesteur plus gros, mais nous proposons les deux options. »
« L’incorporation d’une partie du postdigesteur permet de réensemencer le digesteur en bactéries, reprend Frédéric Page. Mais le postdigesteur a d’autres avantages : lors de l’exploitation, il permet par un jeu de transfert avec le digesteur de nettoyer celui-ci sans interrompre la production et sans casser la vie bactérienne. Le postdigesteur permet aussi de traiter un volume supérieur. Comme nous sommes partis sur la cogénération (l’injection était peu fréquente lors de la conception de notre unité), nous avons opté pour une méthanisation thermophile (52 °C), la chaleur nécessaire étant récupérée sur moteur des cogénérateurs, avec un temps de séjour du digestat assez court, de 35 à 40 jours. » Pour valoriser encore mieux la chaleur, le GAEC prévoit dans une deuxième phase du projet la mise en place d’un équipement en aérothermie des porcheries, ainsi qu’un séchoir multiproduit. « Le troisième objectif auquel répond la méthanisation est de mieux valoriser notre fumier. Grâce au digestat, nous supprimons une bonne part d’apport d’ammonitrate. Une grande partie de l’azote devient ammoniacal et cela crée un effet boost sur nos cultures. Un engrais de bonne qualité avec un épandage qui doit être adapté. Cela nous permet aussi de ne pas dépendre des cours du pétrole. »
Après une mise en charge progressive avec du lisier en décembre 2018, les intrants solides ont été incorporés mi-janvier. Mi-février, la température de croisière de 52 °C était atteinte. La cogénération a été mise en service en mars avec 62 % de charge, soit 110 kW, puis 84 % en avril et 93 % en mai (163 kW). Le business plan avait prudemment estimé la production à 150 kW sur 8 000 h, soit 1 200 MWh/an. La production atteint en fait 167 kW et tourne à 700 h/mois aujourd’hui.
Exploitation : la clé du succès
La clé d’une bonne production, en plus d’une conception bien pensée, vient ensuite de l’exploitation. Une bonne formation à la conduite d’une unité de méthanisation est indispensable. Elle se fait auprès de la chambre d’agriculture, de l’AAMF, en tenant compte des retours d’expérience. « La connaissance des vaches laitières sert aussi : un digesteur a des points communs avec les bovins. Il faut s’imprégner de son unité, se l’approprier, indique Frédéric Page. Le suivi de l’exploitation est primordial : je passe 1 h 30 chaque jour pour suivre et exploiter l’unité. Nous avions prévu un mi-temps dans le business plan, c’est bien le minimum. Nous sommes deux à pouvoir gérer l’unité, mais toutes les personnes travaillant au GAEC ont une connaissance minimum. Le suivi de la biologie à l’aide d’un titrateur FOS/TAC et des analyses régulières en laboratoire sont des outils nécessaires pour corriger la ration si besoin est. J’essaie toujours d’améliorer le processus », conclut Frédéric Page.